Digital ER&D
Computer Aided Engineering
Unlocking the power of simulation, our industry - leading services harness the capabilities of Finite Element Analysis (FEA), Computational Fluid Dynamics (CFD), and beyond. From optimizing product designs to tackling complex engineering challenges, we offer a comprehensive suite of services tailored to your needs.
Why Us?
Our services designed to support companies in their digital transformation journey. The solution combines deep engineering expertise with cutting-edge digital technologies to help companies innovate, optimize, and accelerate their product development processes.
We helps companies innovate by leveraging advanced digital technologies. These technologies enable companies to develop innovative products and services that meet the evolving needs of their customers.
Our services help companies optimize their product development processes, reducing time-to-market and costs. By streamlining workflows and leveraging digital tools, companies can achieve greater efficiency in their operations.
By using advanced simulation and modeling techniques, we helps companies ensure the quality and reliability of their products. This includes identifying potential issues early in the development process and optimizing designs for performance and durability.
Our services help companies reduce costs by optimizing product designs, streamlining processes, and minimizing the need for physical prototypes. This can result in significant cost savings over the product lifecycle.
By partnering with SPIREDGE, companies can gain a competitive advantage in the marketplace. SPIREDGE's expertise in digital technologies and engineering allows companies to differentiate their products and services, attracting more customers and increasing market share.
Workflow
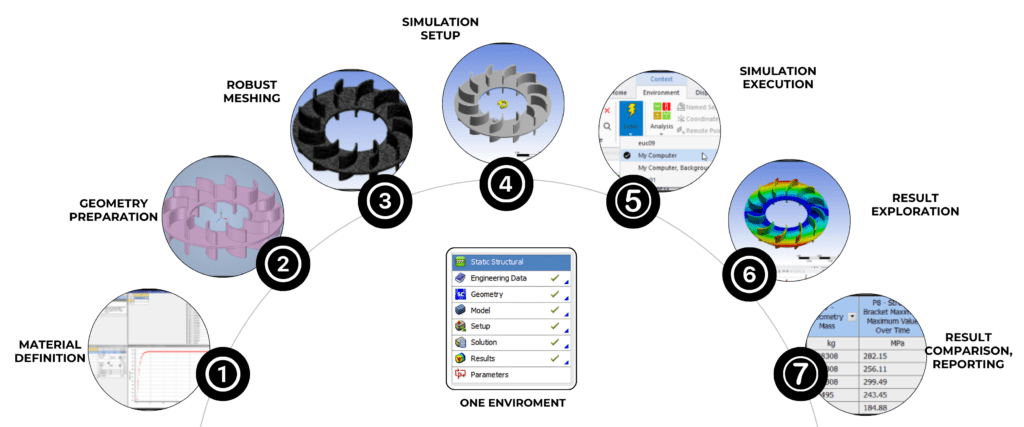
FEA – Finite Element Analysis
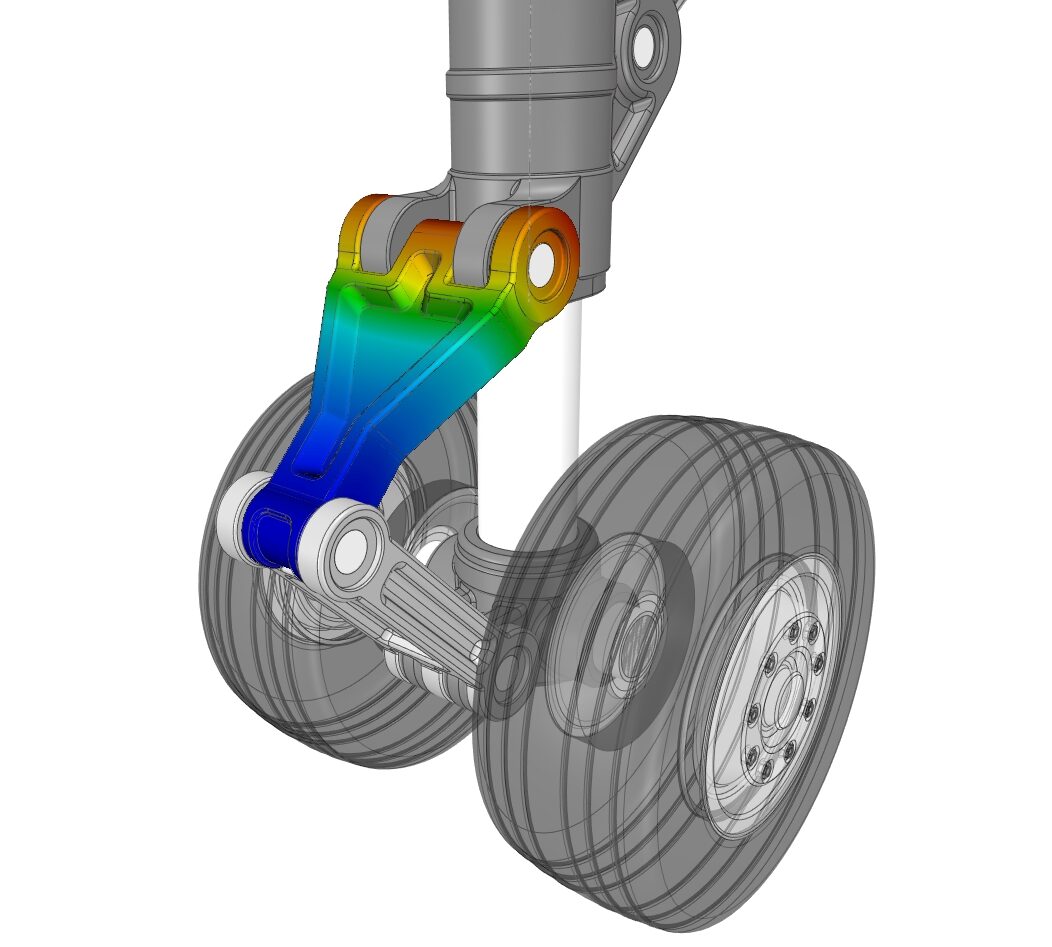
Vibration Simulation
Our expertise lies in scrutinizing the vibration patterns
within a system to pinpoint any irregularities or shifts.
We specialize in assessing the intricate details of
vibration signals, meticulously analysing their
fluctuations and nuances.
Vibration in engineering can compromise structural
integrity, affect performance, and shorten product
lifespan through accelerated wear.
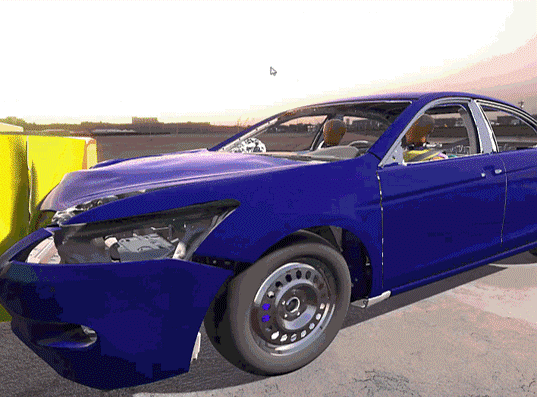
Impact & Deformation Analysis
The Ansys explicit dynamics suite enables you to capture the physics of shortduration events for products that undergo highly nonlinear, transient dynamic forces and get an insight on how a structure responds to severe loadings.
- Severe loadings cause major deformation.
- Stress & Strains
- Failure prediction
- Impact
- Explosive Loading
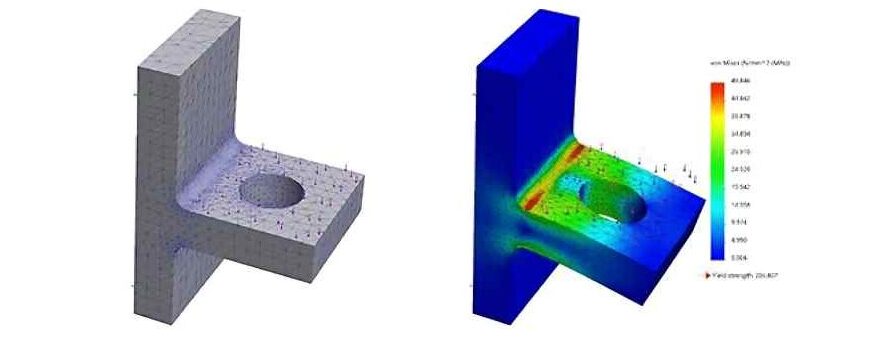
Structural Analysis
We provide advanced simulation tools and expertise to accurately model and predict the behaviour of your structures under different conditions. Our analysis helps optimize designs, ensuring they meet safety standards and performance requirements while minimizing material usage and costs.
- Visualize stress, deformation, failure areas.
- Safety factors ensure load withstandability.
- Displacement data evaluates stability, integrity.
- Dynamic analysis reveals vibration, resonance
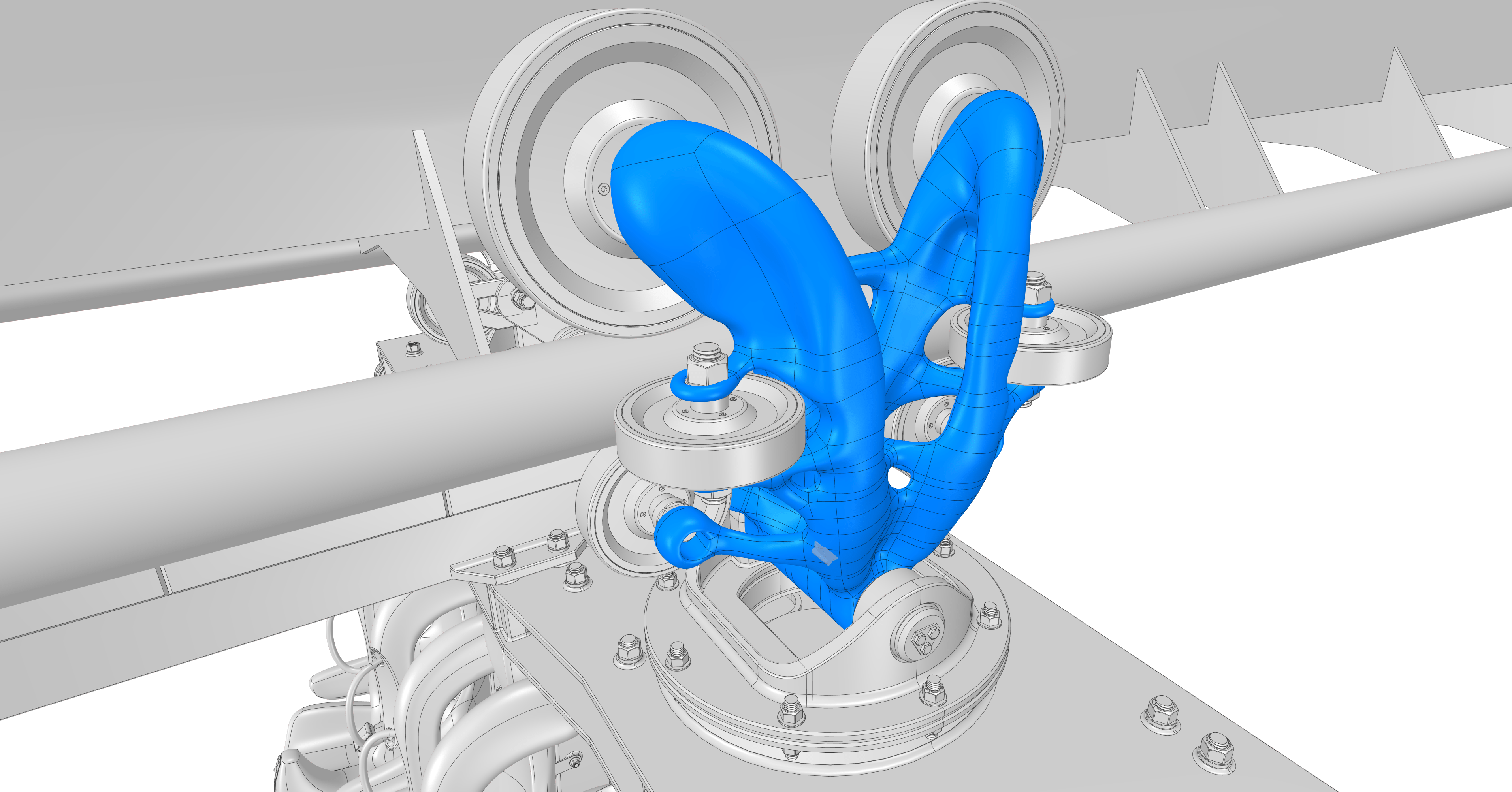
Fatigue and
Durability Analysis
(Life Cycle
Prediction)
Fatigue analysis evaluates how repeated loading affects a structure over time. For
deterministic vibration and constant stress amplitude, engineers use the S
-
N curve of
the material to predict the number of cycles to failure. This process incorporates
lifecycle prediction and durability assessment, considering factors like variable loading,
environmental effects, and material degradation. By integrating these factors,
engineers design more resilient structures with longer lifespans.
- Stress - Life Approach for High - Cycle Fatigue
- Strain - Life Approach for Low - Cycle Fatigue
- The relationship of loading to fatigue failure is captured with a Stress - Life or S - N Curve
- Stresses, strains, and deformation
- Contact Tool results
- Stress Tool
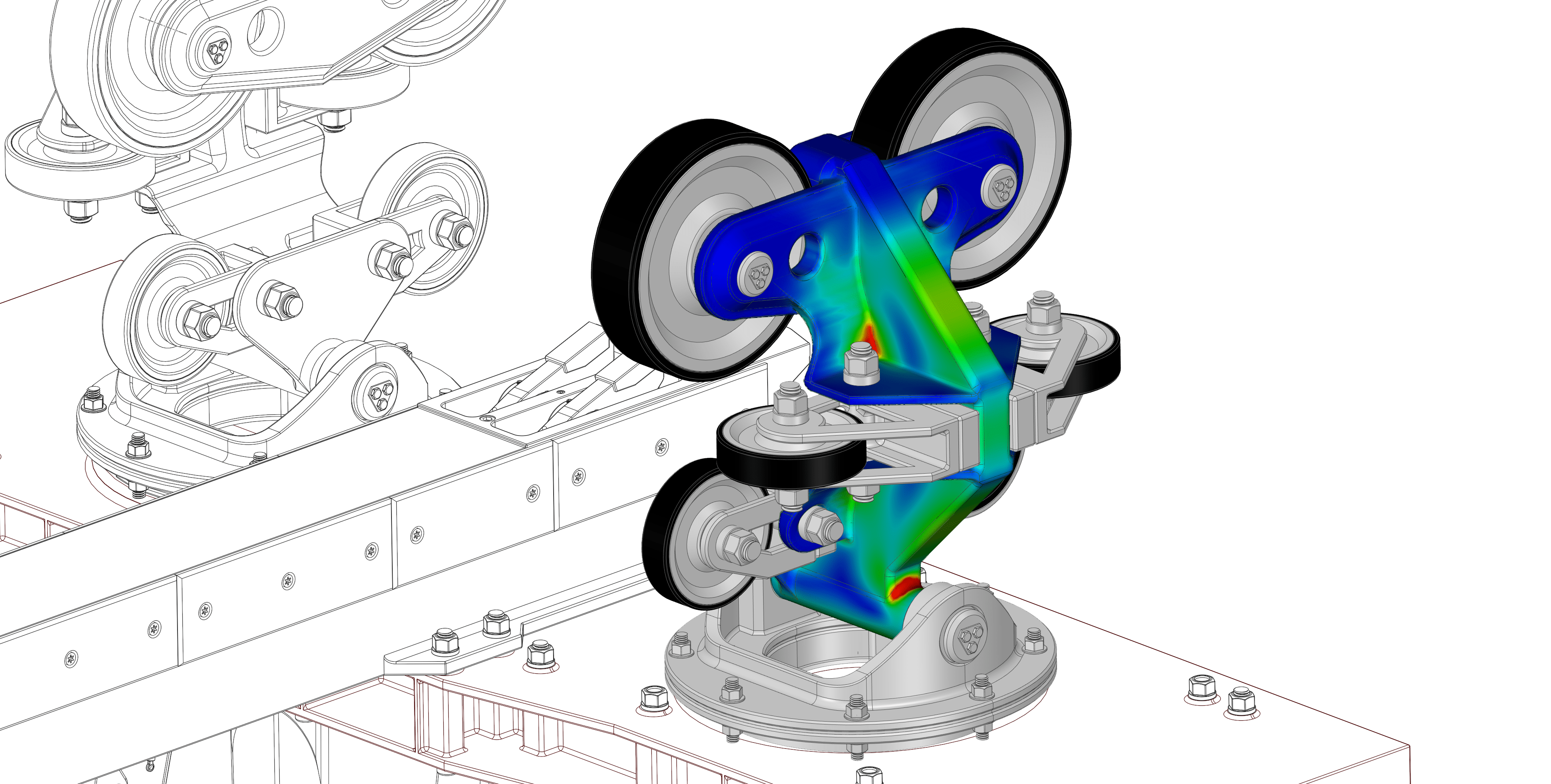
Multi Body Dynamics Simulation
Multibody simulation analyses the dynamic behaviour of interconnected bodies, including rigid and flexible components, constrained by joints. It's used for various systems like automobiles, aircraft, robots, and space structures with large rotations, displacements, and finite strain effects.
- Modelling the flexible, rigid, and joint components
- The finite element mesh automatically represents the geometry while the large deformation/rotation effects are built into the finite element formulation
- Inertial effects are simplified using consistent mass formulation
- Interconnection of parts via joints is simplified
- The parameterization of the finite rotation has been well documented
- Model the material behaviour of the flexible components
- Modal and transient dynamics capabilities to analyse the spatial and temporal effects in a multibody simulation
- Extensive postprocessing capabilities are also available to interpret the analysis results
CFD – Computational Fluid Dynamic
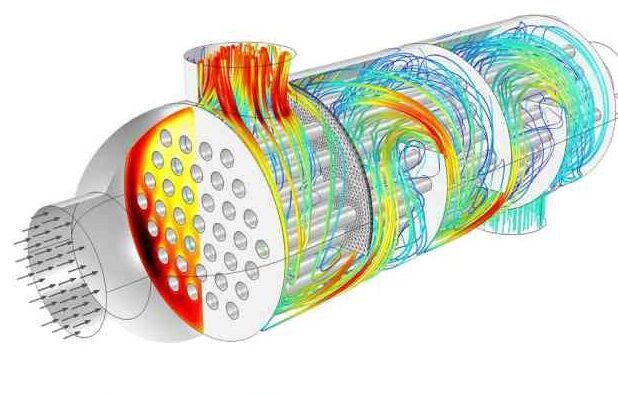
Heat Transfer Analysis
By employing Heat Transfer analysis, engineers can optimize thermal management strategies, predict temperature variations, and evaluate material performance under different thermal loads. This enables the design of reliable systems that can withstand extreme temperatures and thermal cycling while maintaining operational efficiency.
- Temperature distribution throughout system.
- Thermal analysis reveals structural integrity.
- Transient analysis captures system responses.
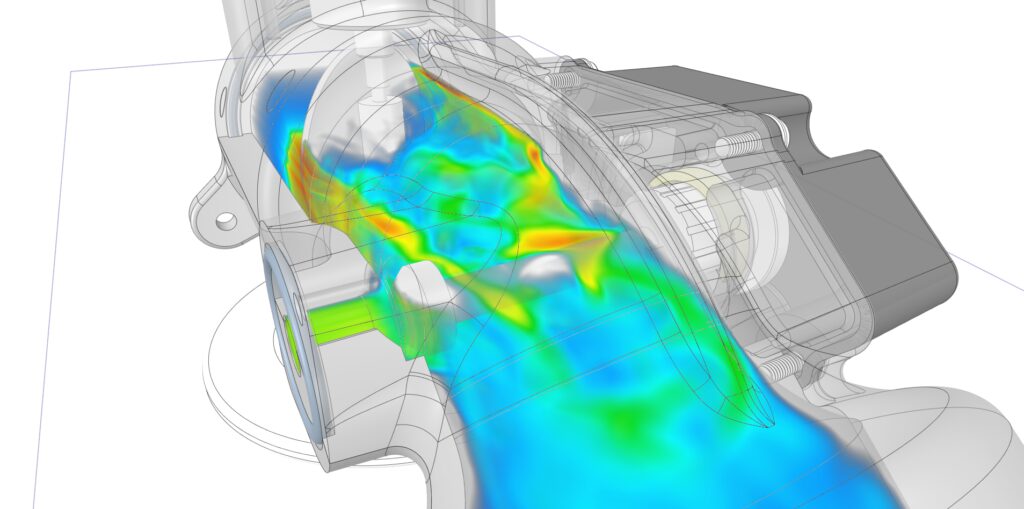
Fluid Structure Interaction
Fluid - Structure Interaction refers to the interaction between a fluid medium and a deformable structure, where the fluid exerts forces on the structure, causing deformation, and the structure affects the flow characteristics of the fluid. This interplay between fluid and structure is crucial to design reliable and efficient engineering systems.
- Analyzes laminar, turbulent, multiphase flow.
- Simulates multiphase flow, studies droplets.
- Simulates heat transfer, considers gradients, fluxes.
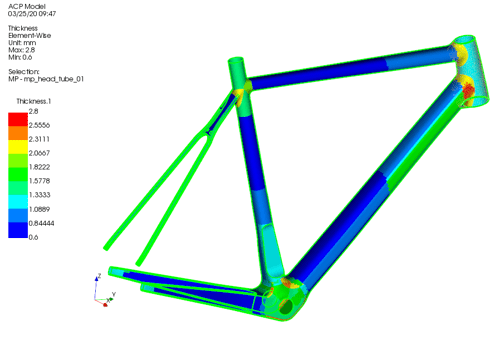
Aero Dynamics Simulation
Aerodynamics simulation plays a crucial role in understanding and optimizing airflow around objects, vehicles, or within systems. Through flow visualization techniques, simulation tools provide a clear understanding of airflow patterns, identifying areas of high drag, lift, or pressure gradients.
- Identifies high and low velocity impact.
- Pressure variations reveal lift, drag impact.
- Streamlines depict flow paths and direction.
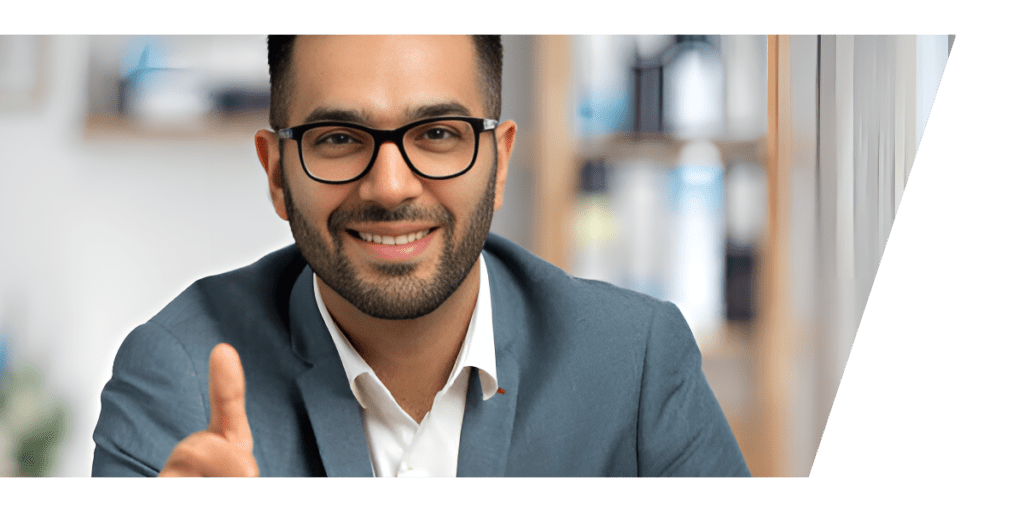
Our Digital ER&D Solution
We specialize in providing engineering solutions that empower our customers to conceptualize, design, and develop superior products, paving the way for a more sustainable future.
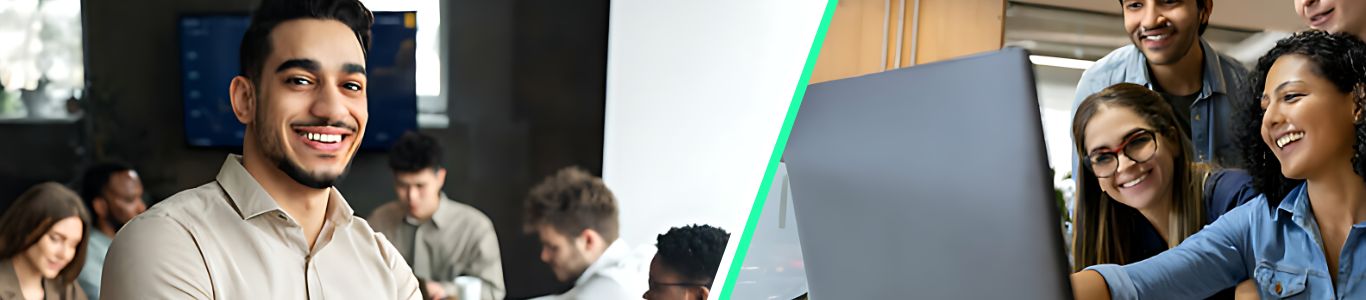
Enabling Innovation
Let 's Connect
Reach out today and explore how we can assist you in Enabling Innovation